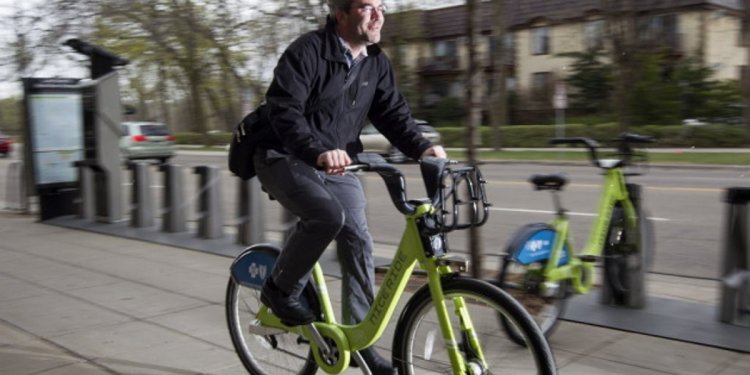
Equipment Supplier Harlow Essex
Harlow Group: sustainability at the heart of expansion for precision metal manufacturer
Harlow Group is one of more than 100 smaller manufacturers that IfM ECS is working with as part of the PrISMS programme – and this case study highlights the difference it has made. It is a leading precision sheet metal manufacturer offering a complete range of fabrication services from laser cutting and CNC punching through to welding, fabrication, finishing and assembly. It operates across sectors including automotive, construction, electronics, medical, retail, transport and telecommunications.
build an extension with environmental considerations at its core |
consider whole-life costs when investing £500k in new technology |
reduce energy costs by £25, 000 a year |
revise the factory layout to achieve greater efficiencies |
increase turnover by 5% per annum |
increase the number of employees by 7% |
analyse market sectors to identify future opportunities. |
The Harlow Group can trace its origins to 1971 as a small sheet metal company in north London. It moved to Harlow, Essex, in 1975, where it has continued to grow in size, service and reputation to become a leading precision sheet metal manufacturer. It has more than 100 employees and 60, 000 square feet of manufacturing space. Its turnover exceeds £8m.
The company offers a complete range of fabrication services from laser cutting and CNC punching through to welding, fabrication, finishing and assembly. It also offers services for new products from initial concept through design and development to final production.
It operates across sectors including automotive, construction, consumer and industrial electronics, medical, retail, transport, telecommunications and vending. It is accredited to satisfy the rigorous demands of the defence and aerospace markets. The company has a business project team to assist clients at all stages of project development.
The firm is committed to investing in staff development and the latest technology to ensure it remains competitive and at the forefront of sheet metal manufacturing. An example is the opening in early 2014 of a 5, 500 square foot extension and the introduction of fibre laser technology to significantly increase manufacturing capacity, along with other changes to improve workflows.
Working with IfM ECS
IfM ECS assessed the firm’s priorities and practices through the IfM ECS Prioritisation process, a whole-business diagnostic and action planning tool. This process highlighted the need to optimise the performance of the existing factory layout and equipment; to plan and implement preventative maintenance, particularly on the most expensive and newest equipment; and to measure the return on investment on new equipment.
Two Masters degree students from the University of Cambridge, under the supervision of one of the IfM ECS team, undertook an extended project to assess the plant layout and work flows and propose alternatives to maximise efficiencies and incorporate the space in the new factory extension.
It was recognised that the company would benefit from specialist advice to help improve both its energy usage and environmental impact. This advice was provided by Ecopare, a project partner of IfM ECS in PrISMS, and it helped the company to make environmental factors and sustainability central to its specifications for the new extension.
This engagement also helped the company to make a more informed technological and economic assessment of the costs and performance of alternative machinery to equip its new extension, enabling it to choose the option with the lowest overall total cost of ownership.
IfM ECS provided support with strategic market analysis to identify a number of opportunities in a wide range of potentially new markets. This allows the firm to target these opportunities to utilise the additional capacity created within the plant.
New machinery, greater capacity
IfM ECS worked closely with the firm as it embarked on a significant investment in equipment and an extension, a review of its factory layout and work flows, and identifying new market opportunities. These interventions, and the results they have brought about, are detailed below.
Strategic planning: Directors have prioritised the firm’s key challenges and formulated an action plan |
|
Jobs created: Staff levels have risen from 103 in November 2012 to 110 in January 2015, an increase of 7% |
|
Financial improvements: Turnover has increased by 5% per annum |
|
Energy savings: Electricity costs have been reduced by £25, 000 a year. A new heating system and low-energy lighting were installed, the weekend energy base load was reduced and a formalised ‘shut down’ policy for heavy equipment was introduced |
|
Effective maintenance: The firm is implementing a preventative maintenance plan, focused on the most expensive and newest equipment |
|
Measuring return on investment: A new system is in place to monitor and optimise the performance of existing equipment |